316 and 316L are two common stainless steel materials that share similarities while each possessing unique characteristics in terms of composition, performance features, and application fields. This article provides a detailed analysis of the key differences between these two stainless steel grades.
Composition Differences
316 Stainless Steel
316 stainless steel typically contains about 0.08% carbon. Its alloy composition includes 16%-18% chromium and 10%-14% nickel, which form the foundation of its excellent corrosion resistance. Notably, 316 stainless steel also contains 2%-3% molybdenum. As a crucial alloying element, molybdenum significantly enhances the material's resistance to pitting and crevice corrosion in highly corrosive environments containing chloride ions. For instance, in seawater environments with high chloride ion concentrations, the molybdenum content in 316 stainless steel effectively resists corrosion.
316L Stainless Steel
316L is a low-carbon version derived from 316 stainless steel, with its carbon content strictly controlled below 0.03%. The primary purpose of reducing carbon content is to improve weldability. During welding, carbon tends to combine with chromium to form chromium carbides, which reduces chromium content in the heat-affected zone and consequently affects corrosion resistance. The ultra-low carbon content in 316L stainless steel significantly minimizes chromium carbide formation, preserving the corrosion resistance of welded areas. This makes it particularly suitable for manufacturing components requiring welding.
Performance Characteristics
316 stainless steel demonstrates outstanding corrosion resistance due to its high chromium and nickel content, maintaining stability in various corrosive environments. The addition of molybdenum further enhances its resistance to pitting corrosion in highly corrosive conditions. However, it's worth noting that its relatively higher carbon content may lead to chromium carbide formation during welding, which can affect corrosion resistance in heat-affected zones.
In comparison, the most distinctive feature of 316L stainless steel is its ultra-low carbon content. This characteristic not only reduces chromium carbide formation but more importantly significantly improves corrosion resistance in welded areas. This gives 316L stainless steel a clear advantage in welding applications, making it particularly suitable for manufacturing welded components.
Application Fields
With its excellent corrosion resistance, 316 stainless steel is widely used in various corrosive environments such as seawater treatment and strong acid/alkali conditions. It's commonly employed in manufacturing equipment and piping systems requiring high corrosion resistance.
316L stainless steel is primarily used in applications requiring welding processes, including shipbuilding, bridge construction, and pressure vessel manufacturing. In low-carbon environments, 316L demonstrates superior corrosion resistance performance.
In conclusion, while 316 and 316L stainless steels may appear similar, they exhibit significant differences in composition, performance characteristics, and application fields. Only by fully understanding these differences can we make correct selections in practical applications, enabling these two high-quality stainless steel materials to deliver maximum value in their respective suitable fields.
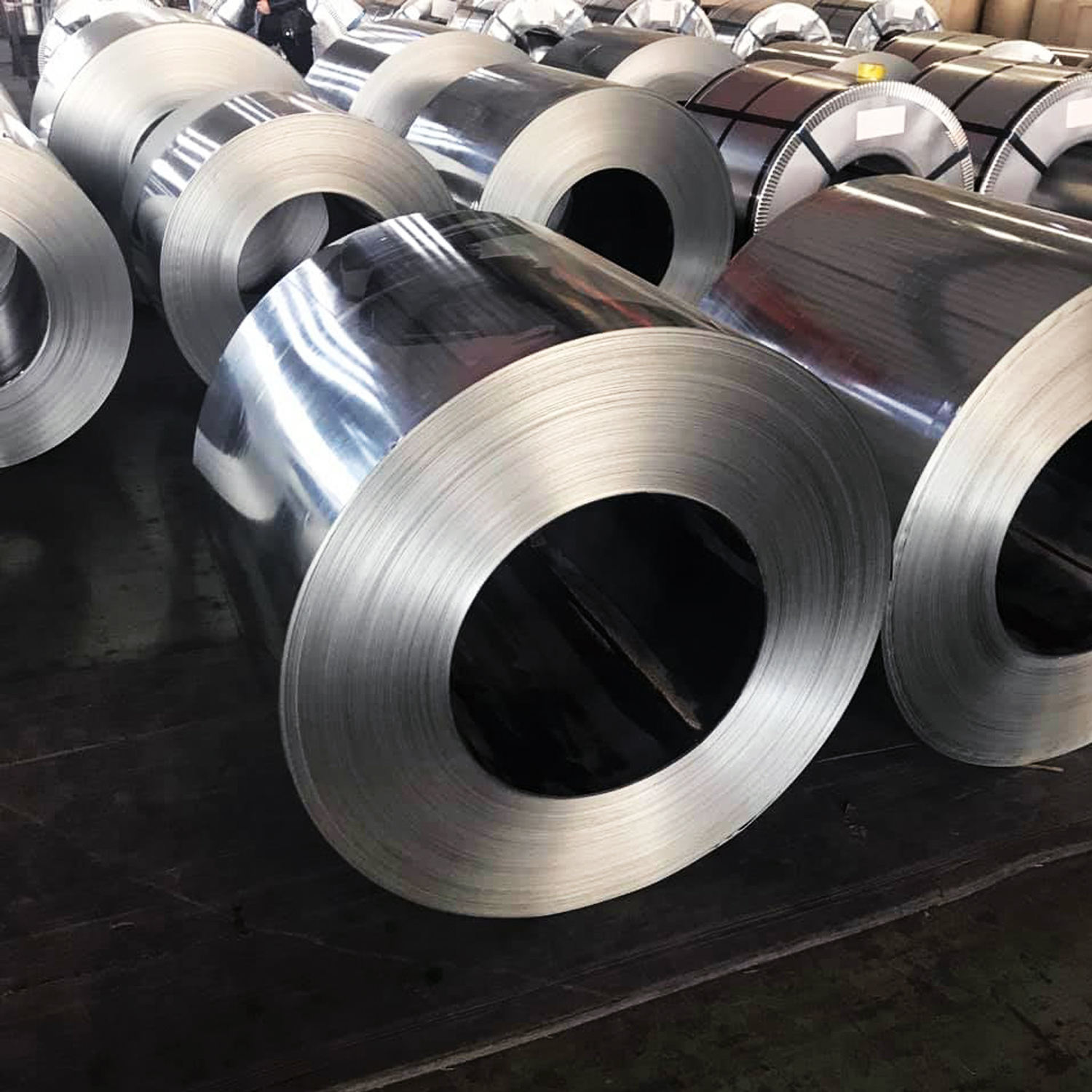
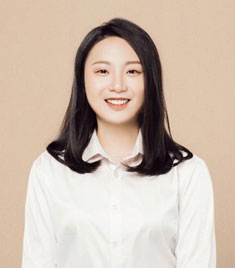
Baoshan District,
Shanghai, China.
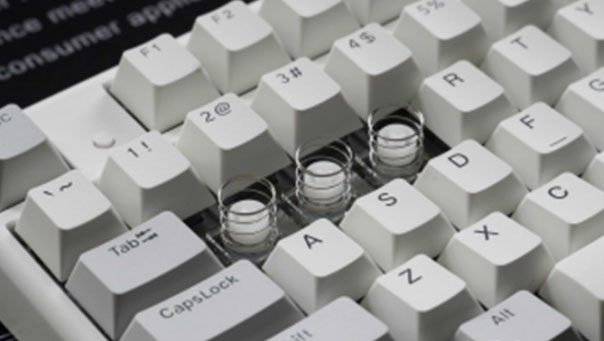